Quality is everyday business for us
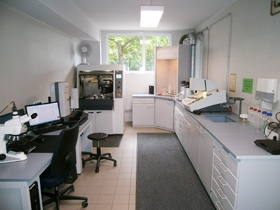
Our quality management system is certified in acc. with DIN EN ISO 9001:2015. Metallographic tests, spectral analyses and hardness tests are performed with laboratory devices that meet today's standard of technology. Computer-assisted material databases that are permanently updated grant us access to all required information. Permanent further education of our employees is our basis for quality-oriented work.
We use all standard hardness test methods:
- Hardness test acc. to Brinell
- Hardness test acc. to Vickers
- Hardness test acc. to Rockwell
- Hardness test acc. to UCI method
- Spectral analysis
- Crack testing using the magnetic powder method
- Crack testing using the dye penetration method
- Determination of surface hardness, nitrogen hardness and case hardness curves
- Metallographic tests
Hardness test
Hardness is the resistance with which a body counteracts the penetration of another. With the most common
hardness test methods, a hard test body is pressed into a test object vertical to its surface.
The hardness value is determined as parameter in hardness testing. It depends on the test method. The statement of the test method must therefore be included in the test result. The test methods differ with respect to shape (pyramid, sphere, cone), material of the penetrating body (steel, hard metal, diamond) as well as the extent and type of impact (static, dynamic).
Hardness test acc. to Rockwell
In 1908, Ludwik published the suggestion to use the penetration depth of a diamond cone for assessment of the hardness of a material and in doing so disable the influence of the sample surface by applying a test preload. Rockwell (USA) turned this idea into a usable hardness testing method in 1931.
The advantage of Rockwell's test is its rapidity.
The most commonly used method in the German
industry is the Rockwell C method.
With the Rockwell C method, a diamond cone is used as
penetrating body (C = cone) with a point angle of 120° and a radius of curvature of 0.2 mm.
Hardness test acc. to Vickers
A hardness test was developed in 1925 based on the ideas of Smith and Sandland in the British Vickers works. It uses a penetrating body in the shape of a four-sided, regular diamond pyramid with a point angle of 136° between opposing surfaces.
The pyramid is pressed vertically into the sample with the test force F (N). The hardness value is calculated from the median of the two diagonals of the impact that occurs during testing.
Hardness test acc. to Brinell
In 1900, Brinell (Sweden) introduced a new hardness test method. In this test, a steel ball with a diameter D is pushed vertically into the level, metallic bright surface of the sample using a test force F. After relaxing, the impact diameter d is measured down to 1/100 mm accuracy (with non-round impact, the median is derived from two diameters standing vertically on each other) and the Brinell hardness calculated (with D and d in mm).
Hardness test acc. to Vickers using the UCI method
The hardness test with the UCI method uses a Vickers diamond as penetrating body. Contrary to the standard Vickers small load method, the Vickers impacts are not evaluated with a microscope but electronically.
The Vickers diamond is attached at the tip of a round metal rod. This metal rod is excited to produce
longitudinal vibrations in its resonance frequency of approx. 78 kHz. The resonance frequency changes when the
Vickers diamond comes into contact with the measuring material. This happens in dependency of the size of the
impact surface of the Vickers diamond. This in turn is the measurement for the hardness of the tested
material. Resonance frequency can be measured very accurately.
This is why the UCI method is
especially suited to simplify and speed up the evaluation of the Vickers impacts and thus the entire test
procedure. The determined measuring value depends on the e-module of the material.